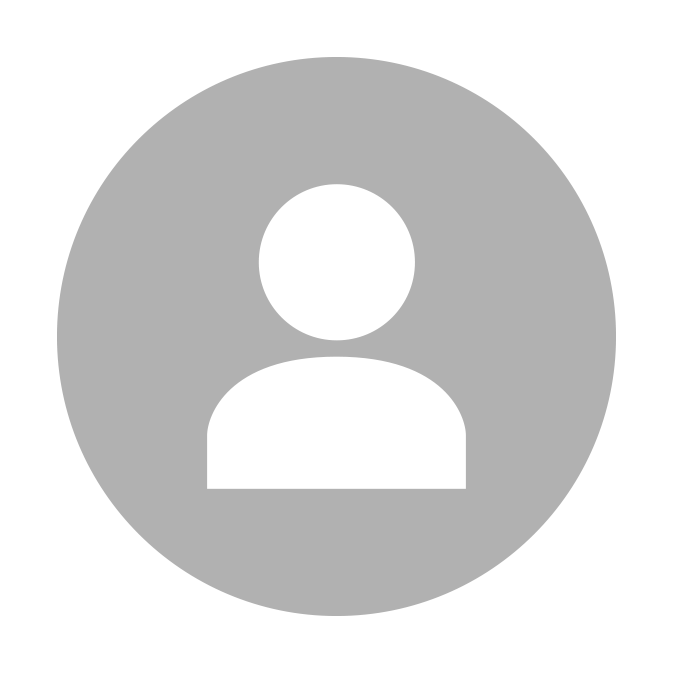
Bradley Bam
Electrical and instrumentation planning for maintanace team. •Senior Training Practitioner for Phenosolvents, Sulphur, Tar and Oxygen generation plants.... | Canada
*50 free lookup(s) per month.
No credit card required.
Bradley Bam’s Emails bb****@su****.com
Bradley Bam’s Phone Numbers No phone number available.
Social Media
Bradley Bam’s Location Canada
Bradley Bam’s Expertise Electrical and instrumentation planning for maintanace team. •Senior Training Practitioner for Phenosolvents, Sulphur, Tar and Oxygen generation plants. Responsible for 64 journey man (junior, senior, specialist and technicians), 6 middle and senior managers, 8 supporting staff, 10 apprentices and 8 university bursary students •Responsible for all safety, functional and technical plant specific training •Responsible for execution, coordinating and arranging of all instrument related training that needs to be done by employees internally and externally •Responsible for execution, coordinating and arranging of all nation safety requirement training (Occupational Health and Safety Act and Internal safety requirements) •Competency testing and declaration of employees regarding safety (works permit acceptance and signing on) •Responsible and accountable for design and implementation of tests for: -Competencies task risk assessments -Works procedures -Apprentice training programs -Bursary student programs •With different plant foremen, identify development gaps for instrumentation journeymen reporting to them. As well as coordinate and arrange the identified training interventions. •Assist management in the development of new works procedures along with the review and improvement of old procedures •Screening and selection of new apprentices that will form part of bursary for instrument journeyman for whole of Sasol Synfuels •Report and write reports on training progress of employees and apprentices and predictive statistics on future training •Coaching and mentoring of apprentices, bursary students and junior journeyman •Responsible to assist journeyman in their upgrading process by identifying and helping to close training gaps as well as building a portfolio of evidence •Attend and screen external training for relevance to journeyman career path. Report back to management on this. •Responsible for all record keeping and reporting of training during holistic workshop and safety audits. • Maintenance of all instrumentation on running plant equipment which included: o Inspections o Reporting of deviations and defects o Works card generation and execution from reports o Sourcing and acquisition of all necessary spares and equipment necessary for repairs o General day to day preventative plant maintenance o Breakdown and emergency defects o Shut down and day to day maintenance (removal, inspection, repair of defects, replacement of broken parts, refurbishment of old parts, reassembly, installation and re-commissioning) o Shut down planning from maintenance perspective: Inventory, stock checking and ordering of spares required for shut down Coordinate pick up, testing, repairing and return of valves, inline flow meters and critical emergency valves with service providers o Mentoring and coaching of instrumentation apprentices • Shutdown maintenance and day to day maintenance on the following equipment: o Control valves o Controllers o Level transmitters o Flow transmitters o Trip systems o Anti-foam dosing pump system o High pressure compressors (ammonia) o Gas liquor separation filters o Phenol extraction systems o Pitch extraction systems o Re-boiler and distillation system o TDC 2000 system, 3000 o Experion • Standby duties. •Establishing of branch: -Sourcing of premises -Buying of office equipment, furnishing and stationary -Staffing which included recruitment and placement of 4 permanent positions and 35 contractor positions -Negotiation, setting up and managing of service agreements with suppliers (importers, shippers, labour brokers, industrial suppliers) •Management -Budget -People management: -Performance management -Remuneration -Staffing and sourcing -Industrial relations (disciplinary enquiry, dealing with labour unions|) -Day to day management -Time and attendance -Legal appointment/ responsibility and accountability for crews working on factory site -Training of staff -Competency assessment and declaration of staff •As combustion specialist: -Co-ordination, planning and supervising of shutdowns on fired combustion equipment -Combustion surveys to determine base line efficiency, flaws and defects in fired furnishes and operating procedures used -Facilitation of combustion fundamentals training for clients -Combustion equipment inspections which include all safety aspects of furnace equipment and the integrity thereof -Combustion related incident investigations which include damage to equipment, injuries to persons or potential loss of life cases -Installation and maintenance of dust filtration systems (self cleaning filter system) -Installation and maintenance of specialised laser gas monitoring equipment (NEO) -Commissioning of H2 electrolysers -Fault finding, repairs, replacement and recommendation on improvements on burner management instrumentation -Installation, maintenance and trouble shooting on boiler tube leak detection system (PROCON based in UK) •Marketing and sales of specialised equipment and after sale technical support •Managing of service agreements •Job costing •Resource management •Forecasting of predicted sales over a 12 month period •Setting up and execution of revised maintenance strategies •Planning all logistics for customer shutdowns. Maintenance instrumentation: -Inspections -Reporting of deviations and defects -Works card generation and execution from reports -Sourcing and acquisition of all necessary spares and equipment necessary for repairs -General day to day preventative plant maintenance -Breakdown and emergency defects -Shut down and day to day maintenance (removal, inspection, repair of defects, refurbishment of old parts, reassembly, installation and re-commissioning) -Shut down planning from maintenance perspective: -Inventory, stock checking and ordering of spares required for shut down Coordinate pick up, testing, repairing and return of valves, inline flow meters and critical emergency valves with service providers -Mentoring and coaching of instrumentation apprentices Shutdown and day to day maintenance: -Control valves -Controllers -Level transmitters -Flow transmitters -Trip systems -ph meters -Density meters -Chemical dosing pump system -Weighing systems -Conveyer belt metal detector system -Lime and water mixing tanks -Steam/electrical coil heating systems -Flame detection and failure systems -Thermal scanning equipment -Exothermic catalyst reactors -Catalyst regeneration systems -Gas fired furnaces -Nuclear source levels -High pressure compressors (hydrogen) Health and safety representative: -Attended all required training -Part of the team that assisted with roll out of the BBS (Behavioural based safety) for the steam station plants -Assisted with all incident investigations on site and help make recommendations on improving safety on site -Part of committee which addressed all requests and complaints from employees concerning health, safety and environment issues -I was elected chairman of the BBS committee for refining. It was our responsibility to roll out the BBS on the business unit. -I did standby for all the refining units on the western factory and was involved in several projects and continuous improvement projects for the instruments on these units.• Maintenance of all instrumentation on running plant equipment which included: o Inspections o Reporting of deviations and defects o Works card generation and execution from reports o Sourcing and acquisition of all necessary spares and equipment necessary for repairs o General day to day preventative plant maintenance o Breakdown and emergency defects o Shut down and day to day maintenance (removal, inspection, repair of defects, replacement of broken parts, refurbishment of old parts, reassembly, installation and re-commissioning) o Checking of mass flow meters accuracy which clients where billed according to o Checking of mass coal weighing system which the plant was billed according to • Shutdown maintenance and day to day maintenance on the following equipment: o Control valves o Controllers o Level transmitters o Flow transmitters o Trip systems o ph meters o Density meters o Chemical dosing pump system o Weighing systems (belt weight scales, load cell systems) o Conveyer belt metal detector system o Lime and water mixing tanks o Steam/electrical coil heating systems o Flame detection and failure systems (Fireye, ultra violet and infra red) o Thermal scanning equipment (to detect leaks or hot spots) o Ammonia gas dosing stations for the reduction of fly ash • Standby duties • Health and safety representative. In this role: o Attended all required training o Part of the team that assisted with roll out of the BBS (Behavioural based safety) for the steam station plants o Assisted with all incident investigations on site and make recommendations on improving safety on site o Part of committee which addressed all requests and complaints from employees concerning health, safety and environment issues • Trained in dust and emissions management and had to make sure that the site complied with the ISO 14000 regulations around all emissions monitoring. • Maintenance of all instrumentation on running plant equipment which included: -Inspections -Reporting of deviations and defects -Works card generation and execution from reports -Sourcing and acquisition of all necessary spares and equipment necessary for repairs -General day to day preventative plant maintenance -Breakdown and emergency defects -Shut down maintenance (removal, inspection, repair of defects, replacement of broken parts, refurbishment of old parts, reassembly, installation and re-commissioning) • Shutdown maintenance and day to day maintenance on the following equipment: -Control valves -Controllers -Level transmitters -Flow transmitters -Trip systems -ph meters -Density meters -Chemical dosing pump system -Batching systems (palletizers, Festo bag packing and weighing machine, hopper batching system) -Weighing systems (belt weight scales, load cell systems) -Conveyer belt metal detector system -Laser inkjet bag printers (DOMINO) • Project work: -Installation and commissioning of level, flow, temperature, and final control valves -Expansion projects -Continues improvement projects -Responsible for factory acceptance tests on behalf of client • Basic first aider for workshop. Within this role: -Attended courses in basic CPR and first aid -Monthly inspections on all first aid kits in work area -Responsible for making recommendation for improving basic health and safety in works area • Basic fire fighter. Within this role: -Part of first response team for small fires -Housekeeping inspections pertaining to fire hazards -Inspection and testing of all fire equipment -Received training in all types of fire extinguisher as well as fixed monitor extinguishers and high pressure hose systems • Standby duties.
Bradley Bam’s Current Industry Suncor Energy
Bradley
Bam’s Prior Industry
African Products
|
Sasol
|
Rand Technical Services
|
SASOL
|
Suncor Energy
Not the Bradley Bam you were looking for?
Find accurate emails & phone numbers for over 700M professionals.
Work Experience

Suncor Energy
E & I Planner
Wed Jan 01 2014 00:00:00 GMT+0000 (Coordinated Universal Time) — Present
SASOL
Learning Practitioner (Instrumentation)
Sun Jan 01 2012 00:00:00 GMT+0000 (Coordinated Universal Time) — Sun Dec 01 2013 00:00:00 GMT+0000 (Coordinated Universal Time)
Sasol
Senior Instrument Artisan
Fri Jan 01 2010 00:00:00 GMT+0000 (Coordinated Universal Time) — Sun Jan 01 2012 00:00:00 GMT+0000 (Coordinated Universal Time)
Rand Technical Services
Project Manager / Branch Manager
Mon Jan 01 2007 00:00:00 GMT+0000 (Coordinated Universal Time) — Fri Jan 01 2010 00:00:00 GMT+0000 (Coordinated Universal Time)
Sasol
Senior Instrumentation Artisan (Journeyman)
Tue Jun 01 2004 00:00:00 GMT+0000 (Coordinated Universal Time) — Sun Jul 01 2007 00:00:00 GMT+0000 (Coordinated Universal Time)
Sasol
Instrument artisan
Tue Jan 01 2002 00:00:00 GMT+0000 (Coordinated Universal Time) — Sat May 01 2004 00:00:00 GMT+0000 (Coordinated Universal Time)
African Products
Instrument Artisan
Mon Jan 01 2001 00:00:00 GMT+0000 (Coordinated Universal Time) — Sat Jun 01 2002 00:00:00 GMT+0000 (Coordinated Universal Time)