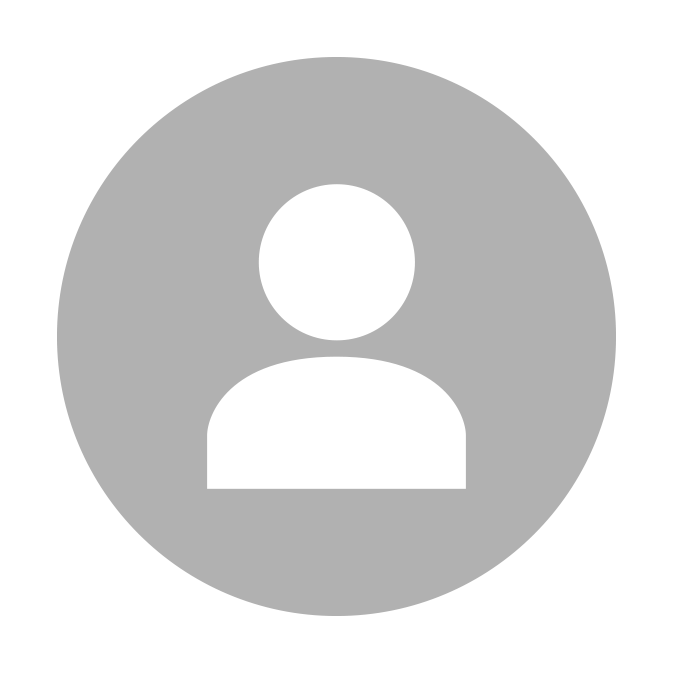
Kevin Lam
•Managed custom machine options with manager (create new options from customer’s requirement, consolidate overlapping options, modularize options to... | Vancouver, Vancouver, Canada
*50 free lookup(s) per month.
No credit card required.
Kevin Lam’s Emails ke****@al****.ca
Kevin Lam’s Phone Numbers No phone number available.
Social Media
Kevin Lam’s Location Vancouver, Vancouver, Canada
Kevin Lam’s Expertise •Managed custom machine options with manager (create new options from customer’s requirement, consolidate overlapping options, modularize options to be configurable, and obsolete options that are outdated or not aligned with design strategy) and review cost and set price of options by extracting ERP data, cross referencing feature/model matrix and marketing feedback •Evaluated special requirements that are out of standard machine specification and offer customized solution from the 800+ existing options •Researched and translated customer's need into design requirements, then redesigned and combined 6 accessory mounts into 1, to simplify product offering, 50% part count and 30% footprint reduction, improve production efficiency, configurable with machine order, became stock-able kit to minimize lead time •Performed tests on competitor tapehead with a focus of customer experience, analyzed adhesion performance of different packaging tape and corrugate grade, analysed tape head wipedown roller dynamic pressure distribution and provided technical data to support marketing campaign •Troubleshoot mechanical, pneumatic, control system failure with service team, came up with temporary quick fix to keep customer’s line running, and communicated with engineering team to create a permanent solution. •Identified production quality issue and critical function features, designed jigs to reject non-conformance parts to be reworked, expedited critical long lead time parts order to avoid production interruption, and provided feedback to vendor on common failure. - Responsible for modifying all mechanical components of a scale down version of existing system, from redesigning parts to overcome space constrain, simplifying assembly process, implementing engineering change from electrical and optical engineers, performing mechanical stress and electric field distribution FEA using COSMOS, reducing cost and preparing all parts and assembly drawings using Solidworks - Designed test jig to perform FMEA on delicate optical sensor, which measures voltage up to 550kV, against shock up to 500G in 3 dimensions - Redesigned sheet metal parts to reduce assembly process and cost while improving strength - Transferred new design specification, assembly procedure and test procedure from engineering to manufacturing include training and follow-up - Hand crafted metal and plastic parts to prove design concept, protect delicate equipment, and improved assembly line safety - Conducted temperature test on plastic parts at -50deg Celsius, and salt fog test on metal parts up to 800 hours according to ASTM B117 to ensure performance in extreme outdoor environment - Assisted senior engineer to create company wide documentation and numbering system - Redesigned and improved wooden shipping crate vibration and shock damping ability by 50% and wrote detail crating instructions to prevent damage to delicate optical components and dielectric silicone shed that insulate up to 550kV. - Assisted Senior Engineer to design a quality control machine that mechanically detects defects on can seam with an accuracy of 0.001 inch at 700 cans per minute, from designing cam actuated mechanism with over 100 parts to simplifying machining procedure, and created SolidWorks models and engineering drawings for its parts and assemblies - Wrote a 30 pages maintenance manual, which includes adjustment procedures and BOM of the can seam defect detector, and created all detailed diagrams - Modified SolidWorks models of ergonomic plastic injection molded consumer can opener to reinforce high stress area, reduced material by 27%, minimize shrinkage problem, and simplify design for in-house manufacturing - Created SolidWorks models of nickel plated cast aluminium commercial can opener for die-casting, investment casting, waterjet cutting, stamping and sheet metal fabrication - Prepared detailed drawings of can openers for design patent application - Modified programs for Programmable Logic Control and its interface that uses proximity and capacitive sensors - Communicated with machinist to reduce machining operations and setup time, and resolve machining problems and tool limitations - Machined parts using CNC and manual lathe, CNC mill, processed parts with sand blaster, tumbler, grinder and buffer, and produce parts with a 250-ton injection moulding machine - Trained assembly line workers to assemble and package consumer and commercial can openers, inspect critical areas, identify failure mechanisms and their repair procedures. NPD programs: -Modified and created new configurations for the next generation power system -Improved reliability by incorporated production feedback and customer suggestions -Defined BOM structure with Manufacturing Engineer and supply chain to optimize production work flow and allow offshore outsourcing -Assisted commodity manager to identify qualified vendor and second source for a critical part -Simplified CSA certification labeling by categorize configurations and assisted compliance engineer to structure CSA certification -Prepared certification prototype and ran tests for different configurations to ensure temperature within limits. Supported NPD programs by • provided DFMA feedback during conceptual, design and prototype phases, • verified assembly documentations from engineering to ensure production needs are met, • created manufacturing plan to engage and align CM, vendor, production, purchasing and engineering Supported custom power system production team by • clarified assembly drawings with design engineer and request drawing update • troubleshot schematics with system engineer and test technician • provided specialized tools for modifying product due to customer request • organized new controller software training, • standardized routing estimation, • developed production documentation collection process, • resolved issues between production team and quality team. Identified a $1.2M potential cost saving opportunity during continuous improvement activity by: • Identified waste on production floor and assembly process due to rework • Extracted pre-rework cost and usage data from ERP system • Estimated modified cost instead of rework with commodity manager • Changed individual packaging to bulk packaging due to customer purchase history and upper level system usage, and reduced shipping and storage cost • Estimated time frame to deplete current stock level with forecasted usage rate • Collaborated with product management, supply chain, production, manufacturing engineering to come up with a strategy to realized the potential saving as much and as quickly as possible To support the organization’s business diversification initiative, during a recent RFQ preparation trip to China, I • Oversaw the local contract design team to finalize the design of a distribution cabinet for the Asia market • Clarified Australian and Singapore customer requirements with the sales team • Worked thru manufacturing challenges during the prototype fabrication • Prepared the prototypes at a Singapore partner site • Answered customer’s design questions during a proof of concept evaluation.@New Product Development team - Developed an indoor vertical distribution bay (BDFB, 24”W x 24”D x 84”H, 160 breaker positions), from design to production • Emphasized DFMA in the design, by incorporate captive features in sheet metal and plastic parts to reduce part count, number and variety of hardware, Z-axis assembly sequence to reduce handling time, resulting in 87% assembly time reduction • Developed innovative “hardwareless” subassemblies to further reduce assembly time, error proof to end user, and improve safety during commissioning • Composed detail work instructions, with assembly pictures, tools list, critical checkpoints, and conducted training to production teams (day shift and night shift), to ensure consistent, quality products are manufactured • Designed single piece flow production line to support a mixed production of 16 configurations, and balanced the build time at each work station with time study result of each assembly step • Identified vendor quality issues with quality team and brain storm temporary solution with design engineering team, then implement in-line checks and assembly update to ensure final product quality @Custom Power System team – • Designed and managed the development of an ultra compact power system by leading a team compose of engineering, compliance, manufacturing and supply chain, from initial product concept, detail design, validation testing, manufacturing introduction, documentation package, service team training to product launch • Expedited a power system prototype to a strategic customer in 9 days, by designing all sheet metal panels and busbars, expedited parts from vendors, assembled the parts, tested the complete system and shipped the prototype overnight @Sustaining team - performed root cause analysis on defective products, considered constraints of repair and retrofit, and provided solutions to alleviate field complications and regain customer confidence.
Kevin Lam’s Current Industry Wexxar Packaging
Kevin
Lam’s Prior Industry
CanPacific Engineering
|
NxtPhase T&D Corp
|
Alpha Technologies Ltd.
|
Wexxar Packaging
Not the Kevin Lam you were looking for?
Find accurate emails & phone numbers for over 700M professionals.
Work Experience

Wexxar Packaging
Senior Mechanical Engineer, P.Eng
Thu Sep 01 2016 00:00:00 GMT+0000 (Coordinated Universal Time) — Present
Alpha Technologies Ltd.
Senior Mechanical Engineer, P.Eng
Fri Apr 01 2016 00:00:00 GMT+0000 (Coordinated Universal Time) — Thu Sep 01 2016 00:00:00 GMT+0000 (Coordinated Universal Time)
Alpha Technologies Ltd.
Manufacturing Engineer, P.Eng
Sat Feb 01 2014 00:00:00 GMT+0000 (Coordinated Universal Time) — Fri Apr 01 2016 00:00:00 GMT+0000 (Coordinated Universal Time)
Alpha Technologies Ltd.
Mechanical Engineer, P.Eng
Sun Mar 01 2009 00:00:00 GMT+0000 (Coordinated Universal Time) — Sat Feb 01 2014 00:00:00 GMT+0000 (Coordinated Universal Time)
NxtPhase T&D Corp
Mechanical Engineer, EIT
Sat Sep 01 2007 00:00:00 GMT+0000 (Coordinated Universal Time) — Thu Jan 01 2009 00:00:00 GMT+0000 (Coordinated Universal Time)
CanPacific Engineering
Mechanical Engineer, EIT
Fri Aug 01 2003 00:00:00 GMT+0000 (Coordinated Universal Time) — Mon Sep 01 2008 00:00:00 GMT+0000 (Coordinated Universal Time)